Dieses Teilprojekt von IntCDC baut auf den Ergebnissen von TP4 der ersten Projektphase auf und erweitert die rekonfigurierbare Fertigungsplattform. Der Schwerpunkt der zweiten Projektphase liegt auf der weiteren Erhöhung der Flexibilität der entwickelten Fertigungsplattform und deren Integration in den Co-Design-Prozess. Die entwickelten Methoden und Systeme werden anhand der Anwendung beim Bau des neuen LCRL demonstriert.
In diesem Projekt arbeitet das ISW mit den Partnern vom Institut für Computerbasiertes Entwerfen und Baufertigung (ICD) sowie dem Institut für Visualisierung und Interaktive Systeme (VISUS) zusammen.
In Teilprojekt 4 wurde in der ersten Projektphase eine neuartige Roboterplattform für die Vorfertigung von Holzbauteilen entwickelt.
Der Grundgedanke hinter dem Konzept ist es, ein modulares, rekonfigurierbares Fertigungssystem zu entwickeln, das entweder direkt auf der Baustelle oder bei lokal ansässigen Holzbauunternehmen für die Durchführung eines spezifischen Projekts aufgestellt wird.
Das Fertigungssystem kann so für jedes Projekt an die spezifischen Anforderungen und Randbedingungen rekonfiguriert werden. Um dies möglich zu machen, sind die Industrieroboter auf Containern nach ISO-668 montiert. Somit können die einzelnen Module des Systems wie herkömmliche Frachtcontainer transportiert, schnell aufgebaut und integriert werden.
Aktuell besteht das modulare Vorfertigungssystem aus 4 Containerplattformen mit Kuka KR420 bzw. Kuka KR210 Industrierobotern. Die Container haben eine Größe von 40 und 20 Fuß und verfügen über Linearachsen mit 10,5 bzw. 4,56 Metern Verfahrweg (ABB. 2).
Dieses Konzept ermöglicht es flexibel mehrere Zellen aus diesen Modulen aufzubauen. Nach dem Aufstellen müssen die einzelnen Container nur mit Strom und Druckluft versorgt werden und sind daraufhin direkt betriebsbereit.
In der ersten Projektphase lagen die Schwerpunkte des ISWs auf der Entwicklung eines geeigneten, rekonfigurierbaren Steuerungssystems, das sich an die Konfiguration des Fertigungssystems anpasst. Ein Task-Skill basierter Aufgabengraph bildet hierbei die Schnittstelle zwischen robotischer Fertigung und computergestütztem Entwurfsprozess.
In der zweiten Projektphase wird die bestehende Anlage um einen neuen schwerlast AMR (Abb. 2) für das Bauteilhandling erweitert, der nun auch die zellenübergreifende Logistik und Fertigung sowie die Vergrößerung des Arbeitsraums einzelner Zellen ermöglicht. Außerdem ist der AMR in der Lage, im Freien zu fahren, so dass Transporte auch außerhalb einer Produktionshalle durchgeführt werden können. Um die autonomen Fähigkeiten des AMR zu realisieren, wird er sowohl hardware- als auch softwareseitig ergänzt. Ziel ist es, das Bauteilhandling durch die Integration des AMR mit den Roboterplattformen und dem Simulationsmodell zu automatisieren. Darüber hinaus soll die Steuerung und rekonfigurierbare Fertigungsanlage in den Co-Design-Entwurf integriert werden.
Zur Sicherstellung der Fertigbarkeit während des Co-Design-Entwurfs wird die Fertigung der Gebäudeelemente aus dem Entwurfsprozess simuliert (ABB. 3).
Dabei werden sowohl die Steuerungskonfiguration als auch das Simulationsmodell modellbasiert generiert. Um eine Integration im Sinne des Co-Designs zu ermöglichen, wird eine Schnittstelle zwischen dem Entwurfsmodell und der Steuerung und Simulation geschaffen (ABB. 4). Dies ermöglicht die automatisierte Simulation vieler Varianten und bildet damit die Grundlage für die Optimierung im Co-Design.
Am Freiburger Zentrum für interaktive Werkstoffe und bioinspirierte Technologien (FIT) wurde 2023 der livMatS Biomimetic Shell Demonstrator gebaut (ABB. 5). Hier wurden die Methoden aus dem TP4 und TP4-2 verwendet, um eine ressourceneffiziente segmentierte Holzschalenkonstruktion zu Fertigen. Die einzelnen vorgefertigten Segmente dieser Holzschale sind demontierbar und wiederverwendbar. Vom Entwurf bis zum fertigen Aufbau wurden Co-Design Methoden angewandt um die Arbeit unterschiedlicher Fachdisziplinen zusammen zu bringen.
Ihr Ansprechpartner
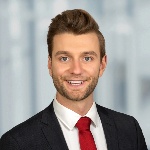
Matthias Marquart
M.Sc.Wissenschaftlicher Mitarbeiter "Industrielle Steuerungstechnik"
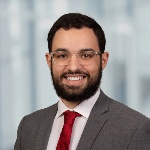
Siddieq Mansour
M.Sc.Wissenschaftlicher Mitarbeiter "Industrielle Steuerungstechnik"