Hintergrund
Kugelgewindetriebe (KGT) sind Maschinenkomponenten, welche zur hochdynamischen und nahezu spielfreien Umwandlung einer rotatorischen in eine translatorische Bewegung und umgekehrt eingesetzt werden. Mithilfe umlaufender Kugeln, welche an Spindel und Mutter abwälzen, können auftretende Kräfte mit gutem Wirkungsgrad sowie vergleichsweise geringen Reibeinflüssen übertragen werden. Neben einer hohen Präzision bei der Bewegungsumwandlung können KGT mit einem sehr guten Preis-Leistungs-Verhältnis überzeugen. Aufgrund ihrer Vorteile gegenüber alternativen Antriebssystemen, wie beispielsweise Lineardirektantriebe oder Zahnstange-Ritzel-Antriebe, bilden KGT nach wie vor die am häufigsten eingesetzte Technologie für elektromechanische Vorschubachsen.
Problemstellung
Werden KGT zur definierten Positionierung eingesetzt, gilt es Nachgiebigkeit und Umkehrspiel im Antriebsstrang zu minimieren. Dazu werden KGT meist initial vorgespannt. Während diese Vorspannung auch durch übergroße Kugeln oder einen Steigungsversatz zwischen den Gewindegängen realisiert werden kann, kommen meist zwei gegeneinander verspannte Mutternhälften zum Einsatz. Für die Dimensionierung der Vorspannkraft gelten konträre Ziele – mit hoher Vorspannung gehen minimales Umkehrspiel und hohe Steifigkeit einher, wodurch gutes statisches und dynamisches Übertragungsverhalten des KGT resultiert. Gleichzeitig steigt jedoch die Reibung, woraufhin Wirkungsgrad und – bedingt durch erhöhte Materialbelastung – Lebensdauer signifikant absinken. Im Stand der Forschung sind bereits einige Ansätze zur aktiven Nachstellung der Vorspannung beschrieben, welche sich jedoch – meist aufgrund von zusätzlichen Kosten, dem Integrationsaufwand sowie negativ beeinflussten Betriebseigenschaften – industriell bislang nicht durchsetzen konnten.
Zielsetzung/Ergebnisse
Im Rahmen dieses Forschungsprojektes soll ein neuartiger passiver Ansatz für eine belastungsadaptive Nachstellung der Vorspannung in KGT-Doppelmuttern erarbeitet und simulationsgestützt dimensioniert werden. Ferner erfolgt die experimentelle Validierung des gefertigten Funktionsmusters an einem Verschleißprüfstand. Übergeordnetes Ziel ist die Verbesserung der Lebensdauer bei gleichbleibendem Betriebsverhalten.
Ihr Ansprechpartner
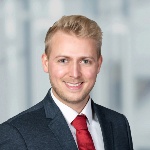
Oliver Jud
M.Sc.Wissenschaftlicher Mitarbeiter "Antriebssysteme und -regelung"