Hintergrund
In diesem Forschungsprojekt wird der Transfer von Erkenntnissen und Forschungsergebnissen des neuen Exzellenzclusters 2075 „Daten-integrierte Simulationswissenschaften (SimTech)“ der Universität Stuttgart in die Industrie adressiert. Um die im Exzellenzcluster neu entwickelten Methoden im Kontext der Industrie nutzen zu können, muss der Wissenstransfer aus der Forschung in die industrielle Anwendung organisiert werden. Hierum kümmert sich das Industrial Consortium SimTech e. V. (IC SimTech) im Rahmen dieses Projektes durch regelmäßige Tagungen, Symposien, Seminarreihen und Workshops. Um Transparenz zwischen wissenschaftlichen Erkenntnissen und industriellen Anwendungen zu schaffen, wird darüber hinaus ein Demonstrator aufgebaut, welcher zeigt, wie neue Methoden zur Integration von Daten in die virtuelle Welt der Simulation zur Steuerung und Regelung realer Prozesse im Kontext der Produktion eingesetzt werden können.
Zielsetzung/Ergebnisse
Forschungsziel des neuen SimTech Exzellenzclusters „Daten-integrierte Simulationswissenschaften“ ist die systematische Integration von verfügbaren Informationen aus gesammelten Daten in den Kreislauf der Systemmodellierung, -simulation und -analyse. Für technische Anwendungen im Bereich der Produktionsautomatisierung ist dieser Ansatz vor allem für Produktionsprozesse sinnvoll, bei denen die Maschinensteuerung sich auf Prozessänderungen während der Produktion einstellen muss.
Diese Anforderung nimmt unter der zunehmenden Individualisierung von Produkten und dem steigenden Trend zu dynamisch ändernden Produktionsumgebungen kontinuierlich zu. Auch der zunehmende Bedarf zur Automatisierung von komplexen Arbeitsschritten, beispielsweise die Handhabung von Gütern mit komplexer Geometrie oder variierenden Formen erfordert zunehmend Automatisierungslösungen die flexibel agieren können.
Ein industrieller Anwendungsfall für einen solchen Produktionsprozesses ist die automatisierte Montage von Leitungssätzen im Automobilbau. Leitungssätze sind, aufgrund der von den Automobilherstellern angebotenen individuellen Konfigurationsmöglichkeit, durch den Endkunden einer enormen Variantenvielfalt unterworfen. Jeder Montagevorgang eines Leitungssatzes im Fahrzeug stellt damit einen individuellen Ablauf mit vollständig neuen Prozessparametern dar. ABB.1 zeigt beispielhaft einen Ausschnitt aus einer Fahrzeugrohkarosse mit einem teilmontierten Leitungssatz.
Da Leitungssätze zudem ein biegeschlaffes Materialverhalten aufweisen, ändert sich ihre Form kontinuierlich während des Montageprozesses und damit auch die relative Lage wichtiger Referenzpunkte wie Stecker oder Befestigungsclips. Für einen automatisierten Montageablauf, beispielsweise durch ein Robotersystem, können somit keine fest definierten Sollpositionen für Griff- und Montagestellen vorgegeben werden. Vielmehr muss die Pose des Leitungssatzes während des Prozesses anhand von Sensordaten, beispielsweise durch ein Kamerasystem, erfasst und geeignete Griffpositionen und Trajektorien für die Montage während der Laufzeit abgeleitet werden. Die eindimensionale Geometrie und große Länge von Leitungssätzen, die auch zu Verflechtungen von Kabelsträngen während der Manipulation des Leitungssatzes führen können, sowie die beständige Änderung von Bezugspunkten, erschweren hierbei die Objekterkennung und die gezielte Manipulation. Derzeit stellt die Leitungssatzmontage damit einen der schwierigsten Prozesse für die Automatisierung in der Produktion von Fahrzeugen dar.
Der im Projekt aufzubauende Demonstrator soll zeigen wie ein Daten-integrierter Simulationsansatz zur Lösung von solchen zentralen regelungstechnischen Herausforderungen eingesetzt werden kann. ABB.2 zeigt eine schematische Darstellung des geplanten Demonstrators. Der Ansatz sieht vor, eine Echtzeit-Simulation des realen Systems, die parallel zum Produktionsprozess abläuft, in die Steuerung zu integrieren. Die Simulation repräsentiert hierbei ein internes Abbild des, für den Prozess relevanten Systemzustands, auf den die Steuerungslogik während des Prozesses zurückgreifen kann. Der Zustand der Simulation wird über aufgezeichnete Sensordaten mit dem realen Prozess synchronisiert. Gleichzeitig werden die aufgezeichneten Sensordaten genutzt, um das Modell, das der Simulation zugrunde liegt, kontinuierlich zu verbessern. Durch einen Vergleich von Modellprädiktion und Messwerten können so prozessrelevante Modellparameter, wie die Steifigkeit des Leitungssatzes, während der Manipulation vom System erlernt werden.
Damit bietet der Demonstrator eine Plattform zum Austausch neu entwickelter Methoden im Bereich Daten-integrierter Modellierung, Simulation und Analyse zwischen den Partnernetzwerken (PN) des SimTech Exzellenzclusters und Industriepartnern des IC SimTech. Synergien im Bereich der Umsetzung des Demonstrators werden hierbei insbesondere in den Partnernetzwerken „Data-integrated model control systems design with guarantees (PN4)”, „On-the-fly model modification, error control, and simulation adaptivity (PN5)”, „Machine learning for simulation (PN6)” und „Adaptive simulation and interaction (PN7)” erwartet.
Mit dem erzielten Wissenstransfer zwischen Forschung und Industrie wird angestrebt, zukünftig vollständig autonom agierende Produktionssysteme realisieren zu können, die in der Lage sind auch komplexe Problemstellungen auf Basis gesammelter Daten eigenständig zu lösen.
Ihr Ansprechpartner
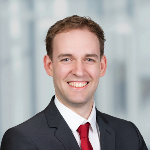
Lukas Zeh
M.Sc.Wissenschaftlicher Mitarbeiter "Antriebssysteme und -regelung"