Hintergrund
Der Prozess einer Maschinen- oder Anlagenerstellung gliedert sich grob in die Phasen der Planung, Konstruktion, Fertigung & Montage sowie der Inbetriebnahme. Eine Virtuelle Inbetriebnahme setzt digitale Simulationswerkzeuge ein, um bereits während der Erstellung Tests zur Identifikation von Fehlern durchzuführen. Ohne eine Virtuelle Inbetriebnahme würden diese Fehler erst nach Aufbau der realen Anlage identifiziert werden, was zu Zeitverzögerungen und hohen Kosten führen würden. Die Virtuelle Inbetriebnahme wird dabei in drei Testkonfigurationen unterteilt, welche in aufeinanderfolgenden Phasen verwendet werden: 1) Model-in-the-Loop, 2) Software-in-the-Loop und 3) Hardware-in-the-Loop. Diese drei Phasen unterscheiden sich insbesondere in der Detaillierungstiefe des vorliegenden Maschinen- oder Anlagenmodells: Während in der rudimentären Model-in-the-Loop-Phase zunächst erste Durchsatzanalysen oder Kollisionsprüfungen durchgeführt werden, können in einem späteren Hardware-in-the-Loop-Test sämtliche physischen Steuerungen auf Fehlverhalten getestet werden.
Problemstellung
Ein Kernproblem in den frühen Phasen der Virtuellen Inbetriebnahme ist, dass Modelle, die sich noch nicht in der Modellbibliothek des Herstellers befinden, zunächst von Grund auf neu modelliert werden müssen. Obwohl sich der Detaillierungsgrad der Modelle in den verschiedenen Konfigurationen stark verändert, unterscheidet sich der strukturelle Aufbau der Modelle nicht signifikant. Es müssen jeweils schon Geometrie, Verhalten und Schnittstellen in den Modellen berücksichtigt werden.
Nach dem aktuellen Stand der Technik existiert oft keine Möglichkeit zum frühen Ablauftest des Gesamtsystems, denn die Modelle sind oft noch nicht von allen beteiligten Herstellern verfügbar. Gründe sind
- sie haben noch gar keine digitalen Modelle im Unternehmen eingeführt
- die Maschine stammt aus dem Sondermaschinenbau und ist eine Erstanfertigung
- Hersteller nutzen unterschiedliche Werkzeuge, wodurch eine Kopplung in einem gemeinsamen Programm nicht ohne Anpassung möglich wird
Die Folge ist, dass die neuen Modelle zunächst aufwändig erstellt werden müssen. Der Fokus der Entwickler:innen liegt somit sehr früh auf der initialen Erstellung von CAD-Modellen, Verhaltensbeschreibungen und Schnittstellen, obwohl zunächst möglichst schnell ein vereinfachtes Modell benötigt wird, um den Gesamtablauf zu validieren. Eine Simulation des Gesamtablaufs kann aber immer erst dann durchgeführt werden, wenn alle Komponenten final modelliert wurden. Die frühe Durchführung eines Gesamtablaufs stellt jedoch einen wichtigen Bestandteil der Simulation dar – das Zusammenspiel aller Teilmodelle kann darin zum ersten Mal getestet werden. Stellt sich dabei heraus, dass einzelne Komponenten falsch modelliert wurden oder aufgrund der Simulationsergebnisse ersetzt werden müssen, kommt es zu hohen zeitlichen Verzögerungen. Dies ist nicht ungewöhnlich, da sich in einem Simulationsmodell sehr oft Teilkomponenten unterschiedlicher Hersteller oder Mitarbeiter:innen befinden, zwischen denen eine Interoperabilität zunächst geprüft werden muss: Es entstehen mehrere Modell-Iterationen, bei denen alle Beteiligten für ihre Komponententests auf die Fertigstellung des Gesamtmodells warten müssen (vgl. Abbildung 1). Eine lückenlose Vorabplanung wird für einen erfolgreichen Einstieg in die Virtuelle Inbetriebnahmen somit eine Grundvoraussetzung. Die hohen Aufwände zur detaillierten Modellierung eines Model-in-the-Loop Simulationsmodells sind ein Problem für die frühe Phase, in der möglichst schnell und aufwandsarm ein Gesamtablaufmodell getestet werden soll. Hier soll im Vorhaben ein intelligenter Assistent zur Modellierung fehlender Komponenten erforscht werden. Unter Einsatz des Assistenzsystems ergibt sich ein Zeitgewinn für den frühen virtuellen Gesamttest (Vergleich Abbildung 1).
Zielsetzung/Ergebnisse
Ziel des Projektes ist die Entwicklung eines KI-basierten Assistenzsystems zur Kompensation fehlender Komponenten in der industriellen Simulation.
Als begleitendes Anwendungsbeispiel (mit ⌂ gekennzeichnet) soll im Folgenden ein einfaches Szenario dienen: Ein fahrerloses Transportsystem soll ein Produkt von einer Fräsmaschine zu einer Abholstation befördern. Mitarbeiter:in A liegt das Modell der Fräsmaschine und der Abholstation bereits vor, das fahrerlose Transportsystem von Mitarbeiter:in B muss jedoch zunächst erstellt werden.
Das Vorhaben AssistVC soll nun den Einstieg in eine frühe Simulation des Gesamtmodells beschleunigen und vereinfachen, indem ein intelligentes Assistenzsystem die fehlende Komponente kompensiert. Dabei entsteht ein (temporärer) Baustein, der schon von Beginn an das Verhalten der Zielkomponente im Gesamtablauf möglichst genau imitiert – eine Simulation der kompletten Anlage wird somit durchführbar. Als Grundlage dient eine bereits vorhandene Prozessbeschreibung der Teilkomponenten, die schon jetzt automatisch in initiale Simulationsmodelle überführt werden kann (vgl. ZIM-AiF „Requirement-Driven Digital Twin (RD-Twin)“, FKZ: KK5311201LF1). ⌂ Das fahrerlose Transportsystem liegt Mitarbeiter:in A also noch nicht als Simulationsmodell vor, ist aber bereits formal beschrieben (Geschwindigkeit, Maße, etc.). Das Assistenzsystem soll nun KI-basiert, unter Betrachtung der Prozessbeschreibung und des Gesamtmodells, Vorschläge zur Verhaltensweise an der nicht modellierten Stelle geben und eigene Unsicherheiten durch gezielte Dialoge eliminieren. Ziel dieser Betrachtung ist es, dass
(1) ein möglichst passendes 3D-Ersatzmodell dargestellt wird (⌂ z. B. strukturähnliches Modell oder identisch dimensionierter Quader als Ersatz)
(2) das Verhalten abgebildet wird (⌂ horizontale Translation) und
(3) eine logische Verknüpfung zu den beteiligten Modellen hergestellt wird (⌂ Produktaufnahme und -übergabe sind Verknüpfungspunkte, deren Steuerung abhängig von dem fahrerlosen Transportsystem sind).
Da sich zu Beginn der Virtuellen Inbetriebnahme Anforderungen noch häufig ändern, soll das System außerdem
(4) mit Hilfe eines Update-Mechanismus Komponentenwechsel intelligent verarbeiten (⌂ das fahrerlose Transportsystem erfüllt die Kundenanforderungen nicht und wird durch ein neues Transportmittel, z. B. ein Förderband, ersetzt).
Ihr Ansprechpartner
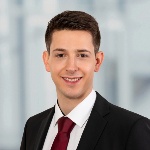
Erik-Felix Tinsel
M.Sc.Wissenschaftlicher Mitarbeiter "Virtuelle Methoden in der Produktionstechnik"