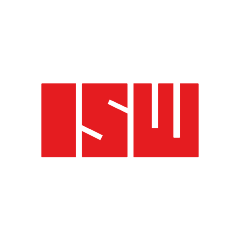
Automation meets innovation
The Institute for Control Engineering of Machine Tools and Manufacturing Units (ISW) of the University of Stuttgart is one of the leading research centers in the field of control engineering – from planning to the tool. The ISW does interdisciplinary research in technologies for the future production and automation. For the industry, we have been, for almost 50 years, an innovative and reliable partner for ambitious challenges, from the first idea to the end product.
Get in touch
Holder of the Chair "Control technology and mechatronics for production systems"
Phone:
+49 711 685 82422
Holder of the Chair "IT for Production"
Phone:
+49 711 685 82466
Holder of the Chair "Model-Driven Engineering for Manufacturing Automation"
Phone:
+49 711 685 84624
Managing Chief Engineer
Phone:
+49 711 685 82462
Group Leader "Real-time communication and control hardware"
Phone:
+49 711 685 84528
Academic Senior Councillor, Student Affairs
Phone:
+49 711 685 82403