Project partner
Background
Due to population growth and the increasing scarcity of natural resources, the construction industry is faced with the challenge of increasing construction volume and reducing material consumption. To meet this challenge, it is necessary to accelerate construction processes, increase the efficiency of building components and avoid construction waste. The priority program (SPP2187) started at the beginning of 2020 with a total duration of 6 years in which methods for faster, more precise and resource-efficient construction with concrete components are developed. The core idea is to combine the flow production known from production engineering with the design and manufacturing concepts of structural engineering. The ISW is working on this in a cooperative project with the Institute for Lightweight Structures and Conceptual Design (ILEK) together with about 50 researchers from all over Germany.
Goals
Within the SPP this subproject deals with the investigation of flow production potentials for load-optimized lightweight concrete components. The focus is on the additive production of recyclable formwork and its integration into the flow production chain. The motivation for this innovative process is given by the present predominant production of formwork components. In practice, the formwork plays a key role in the accuracy and quality of the concrete elements to be produced. However, the production process of the individual formwork components is usually not automated, especially in the case of geometrically complex components. The costs incurred are correspondingly high and reusability is usually not possible. The present subproject is intended to counteract both the latter problem and the shortage of resources. The combination of additive manufacturing technologies together with zero-waste, water-soluble material systems is considered to be a promising alternative to conventional formwork production. The manufacturing process is based on powder-bed water jetting technology and is carried out by spraying water onto a mixture of sand and water-sensitive binder, which after hardening takes on a geometrically stable shape.
To a certain extent, the powder-bed process also allows the integration of further production steps. These include automated reinforcement integration and the installation of fasteners (Fig. 1). In order to guarantee the described manufacturing process, various individual components are be designed. This includes the development of the kinematic system, the components of the material supply and processing system as well as end-effectors for the integration of reinforcement and fasteners. For a quality assuring process control a modular, open control system as well as online control methods for the dynamic adjustment of the process parameters are to be developed.
Get in touch
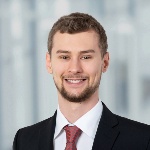
Maximilian Nistler
M.Sc.Group Leader "Mechatronic Systems and Processes"