Background
In the development process of new production plants, simulations are used in various forms in mechanical and plant engineering today, depending on the issue at hand. Simulations help to speed up development and validation processes and increase the quality of systems and the products to be manufactured while reducing costs at the same time. The method of virtual commissioning (VC) of production systems with industrial control systems is of central importance for mechanical and plant engineering. In VC, the control system is coupled with a simulation model of the plant. This allows the control system to be tested safely and comprehensively before the real hardware of the production system is set up.
Problem statement
Parallelization is used to ensure that the simulation reproduces its real counterpart as accurately as possible and that real-time calculation is possible even when using complex models. However, current solutions for distributed real-time simulation for the VC require the model to be split manually between the simulation tasks calculated in parallel. This manual distribution increases the modeling effort and thus reduces the acceptance and cost-effectiveness of real-time co-simulation. In addition, manual allocation requires expert knowledge and does not usually lead to an optimal allocation of the simulation model, as no precise data is available for the calculation effort.
Goals
The aim of this project is to enable automated partitioning for real-time co-simulation in the VC of production systems. This should minimize the manual effort for model partitioning and achieve an optimized model partitioning. The starting point for this novel approach is a functional non-parallelized model for the VC. A partitioning algorithm to be developed in this project divides the overall model into submodels, analyzes the computational effort of the individual submodels and assigns the submodels to different simulation tasks. Depending on the requirements, the partitioned model can be executed with reduced computing time or enable the coupling of different models and simulators.
Get in touch
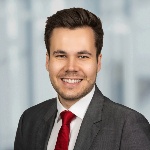
Lars Klingel
M.Sc.Group Leader "Virtual Methods for Production Engineering"

Daniel Littfinski
M.Sc.Research Assistant "Virtual Methods for Production Engineering"