Background
Industrial robots have significant advantages over conventional machine tools in terms of workspace to cost ratio and increased flexibility due to the higher number of degrees of freedom. However, industrial robots are rarely used for applications with high path accuracy requirements, as their accuracy is significantly lower than that of a machine tool.
Problem statement
In order to enable new areas of application for industrial robots, their dynamic path accuracy must be improved. In addition to the hysteresis-related characteristics of the robot joints, a relevant proportion of the position error is caused by the kinematic transmission errors that occur in the robot gears. To compensate these kinematic transmission errors in a model-based manner, all influencing factors (e.g. load, temperature, ...) must be known. The developed compensation approach is intended to work without additional sensors, thus a temperature observer will be integrated.
Goals
As part of the research project, a novel compensation method based on physically motivated and machine learning-based models is being developed to improve the path accuracy of industrial robots. The identification of the kinematic transmission errors and the experimental validation of the compensation method is carried out with a gear test bench.
Get in touch
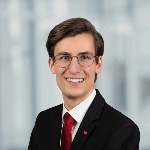
Christian Bauer
M.Sc.Research Assistant "Drive Systems and Motion Control"