Background
In the production of sheet metal parts, the number of variants is increasing due to increasing individualization. As a result, batch sizes are becoming smaller and mold changes more frequent. This results in an increase in scrap, for example due to heating of the tool. Furthermore, dynamic effects, fluctuations in material properties, control deviations and wear-related changes make experience-based predictions of the manufacturing parameters during the production start-up almost impossible. Simulation models can predict the forming result with a high probability. However, there is currently a lack of methods for creating a comprehensive system simulation of a forming press and using it during operation.
Goals
A simulation-based intervention on the control algorithms is to be implemented by means of an in-service system simulation. For this purpose, a real-time capable control-integrated simulation environment for the digital twin of a forming press will be created. The system simulation of the forming press will also be used to create a real-time capable model library for forming technology.
Approach
The digital twin of a production system represents it digitally and is characterized by a bidirectional connection to its real counterpart, which should enable online optimization, among other things. On the way to the realization of a Digital Twin, a real-time co-simulation architecture for control systems is developed. This architecture should enable the implementation of an operational system simulation from machine and process. On this basis, methods for simulation-based control functions can be designed.
Expected Results
The project will develop methods, models and architectures for control-integrated digital twins. For the forming process, success is measured by a significant reduction of the production start-up time after tool change and a real-time reaction of the system to environmental conditions, which leads to the avoidance of production errors.
Get in touch
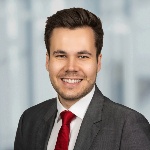
Lars Klingel
M.Sc.Group Leader "Virtual Methods for Production Engineering"